Publicación: Diseño de una extrusora de monofilamento para impresión 3d de diámetro controlado
dc.contributor.advisor | Amezquita Pulido, Manuel | |
dc.contributor.author | Ayala Chauta, Daniel | |
dc.contributor.author | Sierra Velandia, Cristian Eduardo | |
dc.contributor.jury | Reina, Edwin Camilo | |
dc.contributor.jury | Cerón Cortés, Andrés Esteban | |
dc.date.accessioned | 2025-04-03T14:50:45Z | |
dc.date.available | 2025-04-03T14:50:45Z | |
dc.date.issued | 2025-04-03 | |
dc.description.abstract | El presente documento es un paso a paso para diseñar una extrusora de monofilamento de impresión 3D de diámetro controlado, este proyecto nace de una necesidad en el área de polímeros de la universidad ECCI donde se busca incentivar y enseñar a los estudiantes acerca de los procesos de manufactura usados en polímeros, como la extrusión. En la universidad se encuentra un prototipo de extrusora de monofilamento en funcionamiento para uso exclusivo de la institución. Ahora se diseñará una segunda extrusora que será posteriormente fabricada, con la finalidad de complementar la primera y aumentar el número de estudiantes que pueden interactuar con este tipo de máquinas. El documento inicia con una exhaustiva búsqueda de información acerca de los diferentes componentes de una maquina extrusora y su función dentro de la misma, tipos de máquinas extrusoras, polímeros, clasificación, polímeros usados en el proceso de extrusión, manufactura aditiva entre otros temas de interés relacionados. El husillo extrusor es la pieza más importante en cualquier extrusora, por ende, se hace énfasis en el diseño de la geometría y como soportara las cargas aplicadas durante el proceso de extrusión, realizando estudios de movimiento y comprobando la resistencia del material. El diseño del husillo se basará en el libro de transformación de plásticos de V.K Savgorodny, y se modelará posteriormente en el software de ingeniería SolidWorks. Se hará un énfasis en el diseño del barril extrusor y el estudio de transferencia de calor, entendiendo mejor cómo se comportan los polímeros cuando se controlan variables como velocidad de corte y viscosidad, junto con el cambio de la temperatura. Se plantea la geometría, se seleccionarán materiales y especificaran tratamientos térmicos en cada pieza que compone la maquina extrusora, mencionando fabricantes y proveedores de los diferentes componentes comerciales y no comerciales de la máquina. Se realizarán cálculos de transmisión de potencia, selección de motorreductor, selección de cadena y piñones, diseño del conjunto de cabezal y boquilla de extrusión, diseño de unidad de enfriamiento, unidad de halado de filamento y unidad de arrollado para entrega de producto final. El proyecto se dividirá en dos mesas de trabajo. Es decir, se diseñan dos estructuras en perfil cuadrado con su respectiva lamina perforada y asegurada a la estructura, con el fin de sostener y nivelar todos los componentes de la extrusora. Se modelan todos las piezas comerciales y no comerciales de la extrusora en el software SolidWorks y finalmente se ensamblan todos los componentes y unidades en un solo documento 3D. Anexando los planos de fabricación 3D y las fichas técnicas y cotizaciones de los fabricantes y proveedores. Se adjuntan fichas técnicas de calidad, manuales de usuario y mantenimiento y los Scripts de Matlab usados para facilidad de cálculos. | spa |
dc.description.abstract | This document is a step-by-step guide for designing a 3D printing monofilament extruder with controlled diameter. This project arises from a need in the polymer department of ECCI University, where the goal is to encourage and teach students about manufacturing processes used in polymers, such as extrusion. The university currently has a functional monofilament extruder prototype for exclusive institutional use. A second extruder will now be designed and later manufactured to complement the first one, increasing the number of students who can interact with these types of machines. The document begins with an extensive review of information about the different components of an extruder machine and their functions, types of extruders, polymers, classification, polymers used in the extrusion process, additive manufacturing, and other related topics of interest. The extruder screw is the most critical part of any extruder, so emphasis is placed on the design of its geometry and how it will support the applied loads during the extrusion process. Motion studies and material strength tests are performed. The screw design will be based on the book Plastic Transformation by V.K. Savgorodny and will later be modeled in SolidWorks engineering software. Special attention will be given to the design of the extruder barrel and the study of heat transfer, with a better understanding of how polymers behave when variables such as cutting speed, viscosity, and temperature changes are controlled. The geometry will be proposed, materials will be selected, and thermal treatments will be specified for each component of the extruder. Manufacturers and suppliers of both commercial and non-commercial components will be mentioned. Power transmission calculations will be made, along with the selection of the geared motor, chain, and sprockets. The design of the extrusion head assembly, nozzle, cooling unit, filament pulling unit, and winding unit for the final product delivery will also be included. The project will be divided into two workstations. That is, two square profile structures will be designed with perforated plates secured to the structure to support and level all extruder components. All commercial and non-commercial parts of the extruder will be modeled in SolidWorks, and finally, all components and units will be assembled into a single 3D document. 3D manufacturing plans, technical sheets, and quotations from manufacturers and suppliers will be attached. Technical data sheets, user manuals, maintenance manuals, and Matlab scripts used for calculations will also be included. | eng |
dc.description.degreelevel | Pregrado | |
dc.description.degreename | Ingeniero en Mecánica | |
dc.description.tableofcontents | 1 TÍTULO DE LA INVESTIGACIÓN 40 2 PROBLEMA DE INVESTIGACIÓN 40 2.1 DESCRIPCIÓN DEL PROBLEMA 40 2.2 PREGUNTAS DE INVESTIGACIÓN 42 3 OBJETIVOS DE LA INVESTIGACIÓN 43 3.1 OBJETIVO GENERAL 43 3.2 OBJETIVOS ESPECÍFICOS 43 4 JUSTIFICACIÓN Y DELIMITACIÓN DE LA INVESTIGACIÓN 44 4.1 JUSTIFICACIÓN 44 4.2 DELIMITACIÓN 44 5 MARCO DE REFERENCIA DE LA INVESTIGACIÓN 45 5.1 MARCO TEÓRICO 45 5.1.1 EXTRUSIÓN DE POLÍMEROS 45 5.1.1.1 Proceso y equipos de extrusión 46 5.1.1.2 TIPOS DE EXTRUSIÓN 48 5.1.1.2.1 Perfiles sólidos 48 5.1.1.2.2 Perfiles huecos 49 5.1.1.2.3 Producción de láminas y películas 49 5.1.2 MAQUINAS EXTRUSORAS 49 5.1.2.1 Componentes de una maquina extrusora 50 5.1.2.1.1 Tolva de alimentación 50 5.1.2.1.2 Cilindro o barril 51 5.1.2.1.3 Cabezal 52 5.1.2.1.4 Boquilla 52 5.1.2.1.5 Plato rompedor 52 5.1.2.1.6 Husillo 53 5.1.2.2 Tipos de máquinas extrusoras de polímeros 54 5.1.2.2.1 Extrusoras de desplazamiento positivo 54 5.1.2.2.2 Extrusoras de fricción viscosa 55 5.1.3 METODOLOGÍA PARA DISEÑO DE MAQUINAS EXTRUSORAS 56 5.1.3.1 Selección de motor 56 5.1.3.1.1 Gestión inicial 58 5.1.3.1.2 Norma 58 5.1.3.1.3 Lugar de Instalación 58 5.1.3.1.4 Grado de protección 59 5.1.3.1.5 Carga del motor 59 5.1.3.1.6 La red 59 5.1.3.1.7 Arranque 60 5.1.3.1.8 Potencia y eficiencia del motor 60 5.1.3.2 SELECCIÓN DE REDUCTOR 62 5.1.3.2.1 Beneficios del uso de reductores 63 5.1.3.2.2 Como seleccionar un reductor 63 5.1.3.2.3 Factor de Potencia 64 5.1.3.2.4 Tipos de reductores en la industria 65 5.1.3.2.5 Reductores para extrusoras 66 5.1.3.3 DISEÑO DE TOLVA PARA EXTRUSORAS 66 5.1.3.3.1 Criterios de diseño para tolvas y consideraciones importantes 67 5.1.3.3.2 Garganta de alimentación 68 5.1.3.4 METODOLOGÍA PARA DISEÑO DE HUSILLOS 69 5.1.3.4.1 Geometría del husillo 69 5.1.3.4.2 Materiales para fabricación de husillos y tratamientos térmicos 71 5.1.3.4.3 Tratamientos térmicos usados en husillos de extrusión 72 5.1.3.4.4 Control de calidad 73 5.1.3.5 DISEÑO DE BARRIL 73 5.1.3.5.1 Ecuaciones para cálculo de geometría de barril 75 5.1.3.5.2 Esfuerzos en la camisa extrusora 76 5.1.3.5.3 Transferencia de Calor en el barril 76 5.1.3.6 DISEÑO DE CABEZAL 77 5.1.3.6.1 Tipos de cabezal 79 5.1.3.6.2 Unidades que componen un cabezal de extrusión 79 5.1.3.7 DISEÑO DE ZONA DE ENFRIAMIENTO 80 5.1.3.7.1 Geometría de tina de enfriamiento 82 5.1.3.7.2 Control de temperatura 82 5.1.3.7.3 Sistema de Re-circulación y filtración 83 5.1.3.7.4 Facilidad de mantenimiento 83 5.1.3.8 DISEÑO DE ZONA DE HALADO PARA EXTRUSORAS 83 5.1.3.8.1 Materiales de rodillos haladores 84 5.1.3.8.2 Integración con el proceso de extrusión 84 5.1.3.9 DISEÑO DE ZONA DE BOBINADO Y ARROLLADO 85 5.1.3.9.1 Enrollador 87 5.1.3.9.2 Sistema de guiado 87 5.1.3.9.3 Mecanismo de corte 87 5.1.3.9.4 Control de calidad 87 5.1.3.9.5 Facilidad de mantenimiento 88 5.1.3.9.6 Seguridad 88 5.1.4 POLÍMEROS 88 5.1.4.1 Aplicaciones generales de los polímeros 89 5.1.4.2 Clasificación de polímeros 89 5.1.4.2.1 Termoplásticos 90 5.1.4.2.2 Termoestables 90 5.1.4.2.3 Elastómeros 91 5.1.4.3 Comportamiento de los termoplásticos 91 5.1.4.3.1 Efectos de la temperatura 92 5.1.4.3.2 Efecto de la velocidad de deformación 92 5.1.4.3.3 Termo-fluencia y relajación del esfuerzo 93 5.1.4.4 POLÍMEROS USADOS EN EXTRUSIÓN Y SUS CARACTERÍSTICAS 93 5.1.4.4.1 PLA 94 5.1.4.4.2 Nylon 96 5.1.4.4.3 ABS 97 5.1.4.4.4 PMMA 99 5.1.4.5 Estudio reológico en polímeros 100 5.1.4.5.1 La viscosidad 101 5.1.4.6 MANUFACTURA ADITIVA 102 5.1.4.6.1 Principales ventajas de la manufactura aditiva 103 5.1.4.6.2 Limitaciones de la manufactura aditiva 103 5.2 MARCO CONCEPTUAL 104 5.2.1 Conceptos básicos 104 5.3 MARCO LEGAL 110 5.3.1 Normativas Internacionales 110 5.3.1.1 ISO (Organización Internacional de Normalización) 110 5.3.1.2 ASTM International (American Society for Testing and Materials) 111 5.3.2 Normativas Europeas 111 5.3.2.1 EN (Normas Europeas) 111 5.3.2.2 Marking 111 5.3.3 Normativas Nacionales 112 5.3.3.1 ANSI (American National Standards Institute) 112 5.3.3.2 JIS (Japanese Industrial Standars) 112 5.3.4 Normatividad en seguridad y salud en el trabajo 112 5.3.4.1 Normativas internacionales sobre seguridad y medio ambiente 113 5.3.5 Reglamento de Calidad 113 5.3.6 Reglamento Ambiental 113 5.3.7 Propiedad Intelectual 114 5.4 MARCO HISTÓRICO 120 5.4.1 Historia de la extrusión 120 5.4.2 Historia de la extrusión en relación a los termoplásticos 122 5.4.3 Necesidades a las que respondió la invención 123 5.4.4 Extrusión hoy en día 123 6 TIPO DE INVESTIGACIÓN 124 6.1 Estado del arte 124 6.1.1 Patente estudiada N°1 124 6.1.2 Patente estudiada N°2 125 6.1.3 Patente estudiada N°3 126 6.1.4 Patente estudiada N° 4 127 6.1.5 Patente estudiada N°5 128 6.1.6 Patente estudiada N° 6 130 6.2 Requerimientos del cliente 131 6.3 Requerimientos funcionales 132 6.4 Matriz QFD (Quality Function Deployment) 133 6.5 Generación y evaluación de alternativas de diseño 133 6.5.1 Opción 1 de diseño 133 6.5.2 Opción de diseño N° 2 134 6.5.3 Opción de diseño N° 3 135 6.5.4 Opción de diseño N° 4 136 6.6 Definición del diseño dominante 137 6.7 Requerimientos de montaje 139 7 DISEÑO METODOLÓGICO 140 7.1 DISEÑO DE TORNILLO 141 7.1.1 GEOMETRÍA DEL HUSILLO EXTRUSOR 141 7.1.1.1 Relación L/D (Ecuación 4) 141 7.1.1.2 N° Filetes del Tornillo. 142 7.1.1.3 Ángulo de hélice de husillo (Ecuación 11) 142 7.1.1.4 Holgura entre husillo y barril (Ecuación 12) 142 7.1.1.5 Espesor de filete (Ecuación 13) 143 7.1.1.6 Paso de husillo (Ecuación 14) 143 7.1.1.7 Ancho de canal (Ecuación 15) 144 7.1.1.8 Altura filete zona alimentación (Ecuación 6) 144 7.1.1.9 Altura del filete en la zona de dosificación (Ecuación 8) 144 7.1.1.10 Relación de compresión (Ecuación 5) 145 7.1.1.11 Longitud total del husillo 145 7.1.1.12 Longitud zona de alimentación (Ecuación 6) 147 7.1.1.13 Longitud zona de compresión (Ecuación 7) 147 7.1.1.14 Longitud zona de dosificación (Ecuación 8) 147 7.1.1.15 Longitud punta de husillo 147 7.1.1.16 Longitud caja de rodamientos de husillo 148 7.1.1.17 Longitud de cuñero 148 7.1.1.18 Sumatoria de longitudes en el husillo 148 7.1.2 Ecuaciones de diseño mecánico del husillo 149 7.1.2.1 Revoluciones del husillo (Ecuación 16) 149 7.1.2.2 Cálculo del flujo volumétrico o caudal y modelo matemático de la extrusora 150 7.1.2.2.1 Flujo directo 154 7.1.2.2.2 Flujo inverso 155 7.1.2.2.3 Flujo de filtración o fugas 155 7.1.2.2.4 Cálculo de constante de cabezal y boquilla (Kt) 155 7.1.2.2.5 Cálculo de constante geométrica total en conjunto cabezal-boquilla 158 7.1.2.3 Producción de la extrusora 158 7.1.2.3.1 Densidades de polímeros a trabajar 159 7.1.2.3.2 Cálculo de producción de los polímeros trabajados 159 7.1.3 Software MATLAB 160 7.1.4 Cálculo de viscosidad para polímeros 161 7.1.4.1 Cálculo viscosidad ABS 162 7.1.5 Cálculo de diferencia de presión en la extrusora 162 7.1.6 Cálculo de potencia requerida para extrusora 164 7.1.7 Cálculo de potencia requerida para accionar el husillo 165 7.1.8 Cálculo de volumen y masa del husillo 166 7.1.8.1 Material de fabricación del husillo y tratamientos térmicos 167 7.1.8.2 Masa de husillo 168 7.1.8.3 Peso del husillo 169 7.1.9 Estudio de fuerzas en el husillo 171 7.1.10 Torque en el husillo 172 7.1.11 Ecuación diámetro mínimo por estática 173 7.1.12 Cálculo de resistencia del husillo con el método Savgorodny 174 7.1.13 Tensión tangencial máxima sobre la superficie del cilindro 178 7.1.14 Esfuerzo máximo en el rodamiento axial 179 7.1.15 Deformación final en la punta del husillo 180 7.1.16 Solides del husillo será 181 7.1.17 Análisis estático en el husillo extrusor 183 7.1.18 Análisis térmico en husillo 185 7.2 Selección y diseño de cuña 188 7.3 Selección de rodamientos de husillo 188 7.3.1 Ecuación de vida nominal básica según ISO 189 7.3.2 Selección de rodamiento rígido de bolas 190 7.3.3 Selección de rodamiento de rodillos cónicos 192 7.4 Diseño de conjunto caja de rodamientos 194 7.4.1.1 Modelado de estructura de caja de rodamientos 197 7.4.2 Diseño de tapas laterales 199 7.4.2.1 Diseño Tapa lateral izquierda 199 7.4.2.2 Diseño tapa lateral derecha y/o garganta de alimentación 202 7.4.3 Diseño anclaje inferior caja rodamientos 203 7.4.4 Diseño anclaje superior caja rodamientos 204 7.4.5 Separadores especiales caja de rodamientos 205 7.4.6 Selección de retenedores caja de rodamientos 205 7.4.7 Selección de graseras automáticas para lubricación 206 7.4.8 Ensamble conjunto caja de rodamientos 207 7.4.9 Lista de consumibles conjunto caja de rodamientos 208 7.5 DISEÑO DE UNIDAD DE ALIMENTACIÓN Y TOLVA 209 7.5.1 Tolva de alimentación 210 7.5.1.1 Geometría y ángulo de inclinación 211 7.5.1.2 Volumen real del polímero en la tolva 212 7.5.1.3 Relaciones para el cálculo de flujo en tolvas 213 7.5.1.4 Cálculo de esfuerzos en tolvas 214 7.5.1.5 Espesor de lámina para tolva 215 7.5.1.6 Dimensiones y criterios de diseño final en tolva de alimentación 217 7.5.1.7 Modelado en SolidWorks, tolva de alimentación 217 7.5.2 Diseño tapa de tolva 218 7.5.3 Diseño de colector de metales 219 7.5.4 Diseño base superior exclusa 221 7.5.5 Diseño base inferior exclusa 221 7.5.6 Diseño tapa exclusa 223 7.5.7 Diseño de exclusa 223 7.5.8 Barras imantadas 224 7.5.9 Ensamble Conjunto de Alimentación-Tolva 225 7.5.10 Lista de consumibles Unidad de alimentación 226 7.6 Diseño de transmisión de potencia para la extrusora 227 7.6.1 Selección de motor 227 7.6.1.1 Diseño de base para motor 230 7.6.2 Selección de Reductor de velocidad 230 7.6.2.1 Diseño de base para reductor 232 7.6.3 Ensamble unidad de transmisión de potencia 233 7.6.4 Lista de consumibles unidad de transmisión de potencia 234 7.7 Diseño de acople de motorreductor-husillo 235 7.7.1 Selección de cadena 236 7.7.2 Selección de piñones Sprocket 236 7.7.3 Base de conjunto motorreductor 238 7.7.4 Rejillas de protección para zonas en movimiento 240 7.7.4.1 Protector husillo 241 7.7.4.2 Protectores laterales 241 7.7.5 Lista de consumibles base motorreductor 242 7.8 Diseño de barril extrusor 242 7.8.1 Cálculo de diámetro interno del cilindro 243 7.8.2 Selección de material para barril extrusor 243 7.8.3 Cálculo de pared de cilindro 244 7.8.4 Esfuerzos en la camisa del barril 245 7.8.5 Análisis estático en el barril extrusor 249 7.8.6 Estudio de transferencia de calor en el barril y el husillo 251 7.8.7 Balance energético del sistema 252 7.8.8 Cálculo coeficiente de transferencia de calor 256 7.8.8.1 Cálculo de coeficiente de transferencia de calor por convección 256 7.8.8.2 Número de Grashof 257 7.8.8.3 Numero de Rayleigh 259 7.8.8.4 Cálculo de numero de Nusselt 259 7.8.8.5 Cálculo de coeficiente de radiación 262 7.8.9 Pérdidas de calor 263 7.8.9.1 Pérdidas por conducción 263 7.8.9.2 Pérdidas por radiación 264 7.8.10 Cantidad de Calor necesario para elevar el material a temperatura de extrusión 265 7.8.11 Cantidad de energía calorífica en todo el sistema 265 7.8.12 Selección de banda calefactora para cilindro extrusor 266 7.8.13 Modelado del barril extrusor en SolidWorks 268 7.8.14 Análisis térmico del barril 268 7.9 Diseño de conjunto plato rompedor 272 7.9.1 Diseño de placas de acero para conjunto plato rompedor 272 7.9.2 Diseño de platina rompedora 275 7.9.3 Diseño de base para conjunto plato rompedor 276 7.9.3.1 Diseño de base inferior 277 7.9.3.2 Diseño de base superior 278 7.9.4 Ensamble de conjunto plato rompedor 279 7.9.5 Lista de consumibles del conjunto plato rompedor 280 7.10 Diseño de boquilla y cabezal 281 7.10.1 Ensamble del conjunto Cabezal-boquilla 284 7.11 Diseño de sistema de calibrado 284 7.11.1 Diseño de dado de calibración 284 7.11.2 Diseño de base inferior para dado de calibración 286 7.11.3 Diseño de base superior dado de calibración 287 7.11.4 Ensamble de unidad de calibración 288 7.11.5 Lista de consumibles unidad de calibración de filamento 289 7.12 Sistema de Medición digital. 290 7.12.1 Medidor de diámetro Zumbach ODAC 18XY 290 7.12.1.1 Características especiales de ODAC 18XY 290 7.12.1.2 Ficha técnica del fabricante 291 7.12.1.3 Zumbach ODAC 18XY 293 7.12.2 Base para medidor de diámetro 293 7.12.3 Ensamble unidad de medición 294 7.12.4 Lista de consumibles unidad de medición 295 7.13 Plancha soporte estructura mesa 1 296 7.14 Estructura mesa de trabajo 1 297 7.15 Ensamble general mesa de trabajo 1 299 7.15.1 Lista de consumibles ensamble general mesa 1 299 7.16 Sistema de Enfriamiento. 300 7.16.1 Tina de enfriamiento 301 7.16.2 Diseño de rodillos tensores de filamento 302 7.16.3 Diseño de bases superiores e inferiores para rodillos tensores 303 7.16.3.1 Base de rodillo Inferior tensado 1 303 7.16.3.2 Base rodillo inferior tensado 2 304 7.16.3.3 Base rodillo inferior tensado 3 305 7.16.3.4 Base superior rodillos tensores 306 7.16.4 Selección de bomba de agua 307 7.16.5 Ángulos de anclaje tina de enfriamiento 308 7.16.6 Ensamble general unidad tina de enfriamiento 309 7.16.7 Lista de consumibles unidad tina de enfriamiento 309 7.17 DISEÑO DE ZONA DE HALADO 310 7.17.1 Diseño de estructura zona de halado 311 7.17.2 Diseño de rodillos de poliuretano 312 7.17.2.1 Rodillo de poliuretano 1 313 7.17.2.2 Rodillo de poliuretano 2 314 7.17.3 Diseño de eje macizo 314 7.17.4 Diseño de brida para apoyo de rodamientos 316 7.17.5 Selección de rodamiento 317 7.17.5.1 Ficha técnica SKF 318 7.17.6 Ensamble general unidad de halado 319 7.17.7 Lista de consumibles unidades de halado 320 7.18 Diseño de zona de arrollado 321 7.18.1 Diseño de eje de doble hélice 322 7.18.2 Diseño de base para eje de doble hélice 323 7.18.3 Diseño de polea unidad de arrollado 324 7.18.4 Diseño de dispositivo móvil zona de arrollado 326 7.18.5 Diseño de tornillo especial para dispositivo móvil 327 7.18.6 Carrete bobinado de filamento 328 7.18.7 Diseño de eje macizo para carrete 329 7.18.8 Selección de rodamiento para eje macizo 330 7.18.9 Selección de motorreductor, unidad de arrollado 332 7.18.10 Selección de poleas para transmisión de potencia Reductor-carrete de bobinado 335 7.18.10.1 Selección de polea conductora 335 7.18.10.2 Selección de polea conducida 337 7.18.11 Selección de correa, transmisión de potencia 339 7.18.11.1 Cálculo de Correa 339 7.18.11.2 Cálculo de la distancia entre centros 341 7.18.11.3 Cálculo de longitud de correa 342 7.18.12 Diseño de bases para unidad de arrollado 344 7.18.12.1 Diseño de base para apoyo eje doble hélice 344 7.18.12.2 Diseño de base para carrete 345 7.18.12.3 Diseño de base reductor 347 7.18.13 Ensamble general unidad de arrollado 348 7.18.14 Lista de consumibles unidad de arrollado 348 7.19 Diseño de planchas unidad de arrollado 350 7.19.1 Diseño de plancha nivel superior 350 7.19.2 Diseño de plancha nivel inferior 351 7.20 Diseño de estructura mesa de trabajo 2 352 7.21 Ensamble general mesa de trabajo 2 354 7.21.1 Lista de consumibles para ensamble mesa general de trabajo 2 355 7.22 Diseño de sistema de control 356 7.22.1 Diseño de base para unidad tablero eléctrico 358 7.22.2 Ensamble de unidad de control de extrusora 359 7.23 Ensamble final de todos los componentes del proyecto 360 7.24 Medidas de seguridad implementadas en la extrusora 362 7.24.1 Protectores laterales 363 7.24.2 Protectores especiales para cilindro extrusor 363 7.24.3 Aviso de seguridad en Gabinete eléctrico 365 7.25 Pruebas mecánicas a piezas y estructuras usando SolidWorks 365 7.25.1 Análisis estático mesa de trabajo N°1 366 7.25.2 Análisis estático mesa de trabajo N°2 368 8 FUENTES PARA LA OBTENCIÓN DE INFORMACIÓN 371 8.1 Fuentes primarias 371 8.2 Fuentes secundarias 372 9 RECURSOS 374 9.1 Recursos humanos 374 9.1.1 Tablas de costo por hora para estudiantes y docentes 374 9.2 Recursos físicos 375 10 CRONOGRAMA 376 11 Presupuesto 378 12 Conclusiones 380 13 Anexos 380 14 Referencias 396 | spa |
dc.format.extent | 400 p. | |
dc.format.mimetype | application/pdf | |
dc.identifier.uri | https://repositorio.ecci.edu.co/handle/001/4436 | |
dc.language.iso | spa | |
dc.publisher | Universidad ECCI | |
dc.publisher.faculty | Facultad de Ingenierías | |
dc.publisher.place | Colombia | |
dc.publisher.program | Ingeniería Mecánica | |
dc.rights.accessrights | info:eu-repo/semantics/openAccess | spa |
dc.rights.coar | http://purl.org/coar/access_right/c_abf2 | |
dc.rights.license | Atribución-NoComercial-CompartirIgual 4.0 Internacional (CC BY-NC-SA 4.0) | spa |
dc.rights.uri | https://creativecommons.org/licenses/by-nc-sa/4.0/ | spa |
dc.subject.proposal | Extrusión | spa |
dc.subject.proposal | Polímero | spa |
dc.subject.proposal | Termoplástico | spa |
dc.subject.proposal | Manufactura aditiva | spa |
dc.subject.proposal | Viscosidad | spa |
dc.subject.proposal | Husillo | spa |
dc.subject.proposal | Barril extrusor | spa |
dc.subject.proposal | Alimentación | spa |
dc.subject.proposal | Impresión 3D | spa |
dc.subject.proposal | Compresión | spa |
dc.subject.proposal | Dosificación | spa |
dc.title | Diseño de una extrusora de monofilamento para impresión 3d de diámetro controlado | spa |
dc.type | Trabajo de grado - Pregrado | |
dc.type.coar | http://purl.org/coar/resource_type/c_7a1f | |
dc.type.coarversion | http://purl.org/coar/version/c_ab4af688f83e57aa | |
dc.type.content | Text | |
dc.type.driver | info:eu-repo/semantics/bachelorThesis | |
dc.type.redcol | http://purl.org/redcol/resource_type/TP | |
dc.type.version | info:eu-repo/semantics/acceptedVersion | |
dspace.entity.type | Publication |
Archivos
Bloque original
1 - 4 de 4
Bloque de licencias
1 - 1 de 1
Cargando...
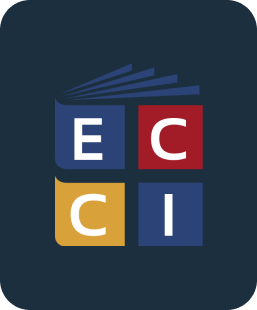
- Nombre:
- license.txt
- Tamaño:
- 15.18 KB
- Formato:
- Item-specific license agreed upon to submission
- Descripción: